Inline SMD soldering with reflow ovens, wave solders or soldering robots
Inline soldering can be performed with various SMD soldering equipment depending of the soldering task
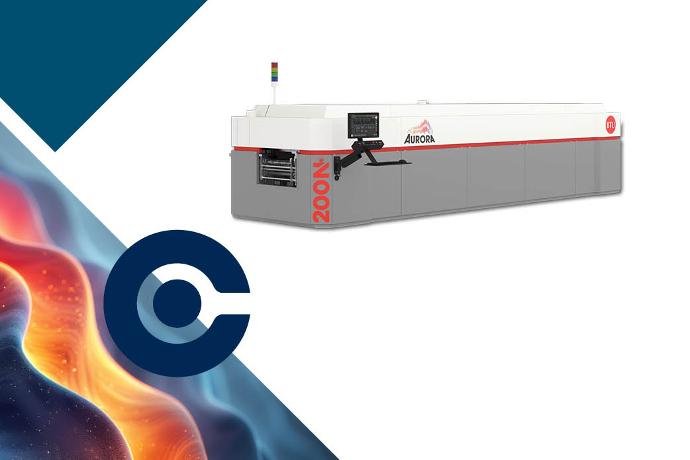
Reflow soldering
Inline soldering with reflow ovens | We offer a full range of BTU reflow ovens to suit any production size and need.
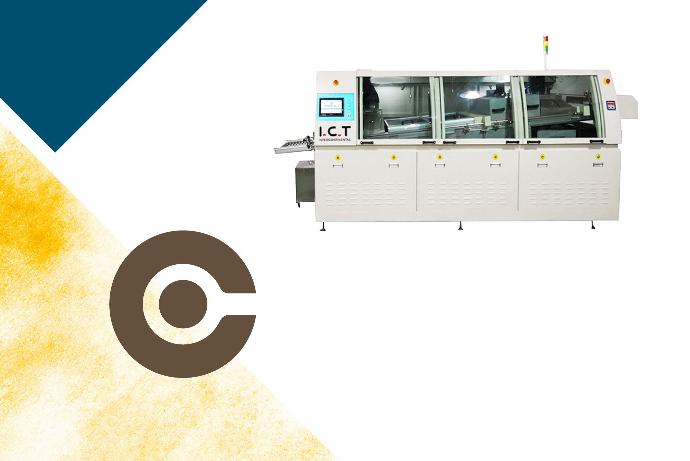
Wave soldering
Wave soldering machines | See our selection of wave solders for Through Hole Technology THT soldering.
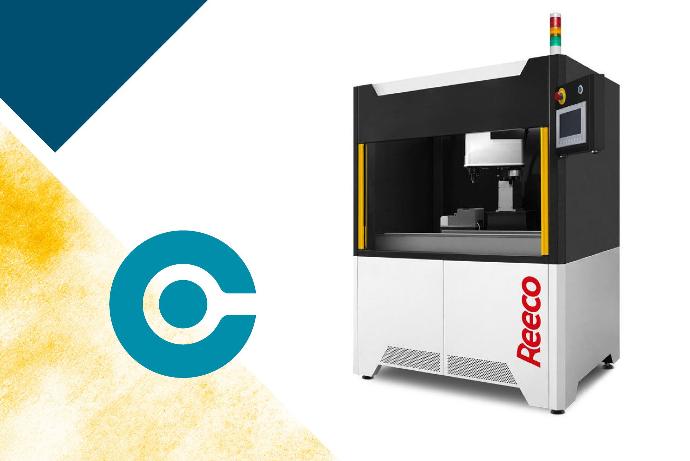
Soldering robot
Inline soldering robot | See this soldering robot that can serve both as an inline soldering robot and a stand alone unit.
Reflow soldering and wave soldering are two very different soldering techniques. Both soldering types are used as PCB assembly line soldering.
Reflow soldering is in most electronics productions, an inline soldering process where components are reflow soldered performed by either hot air or nitrogen.
Wave soldering through hole components are soldered by a solder wave of melted solder. Wave soldering can also be performed in an atmosphere of hot air or nitrogen.
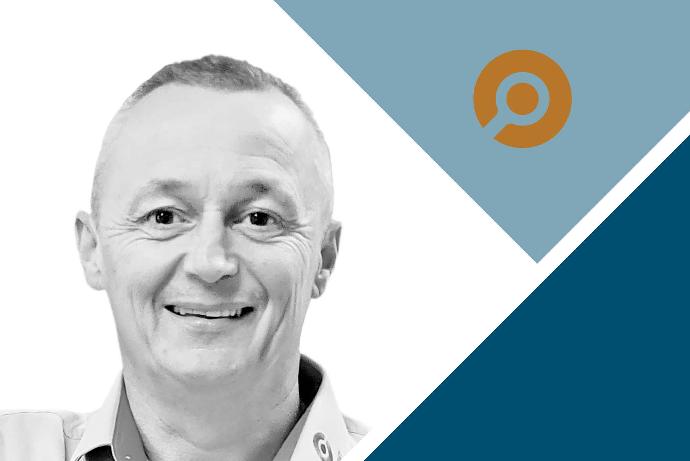
Inline soldering guidance
Steen knows about reflow ovens | It's always nice to talk to an expert that have your best interest at heart.
Soldering guidance >Inline soldering with soldering reflow ovens from BTU International, wave soldering with I.C.T. units and Reeco inline soldering robots.