Accelerate product changeover in solder print process
When assembling boards at high speed on a surface-mount line, and in manufacturing scenarios that involve many changeovers per day, automating as many product changeover tasks as possible can help save time and save human errors that otherwise cause lost production and demand extra time to rectify.
A helpful system such as Automatic Program Change-over (APCO) can accomplish the program change quickly and ensure the correct program is loaded on all machines in the line. As far as component mounters are concerned, it can be possible to setup feeders to handle several products without needing to change them.
When a new feeder configuration is needed, this can be setup offline and the feeders are brought to the machine just in time for the changeover. Auto-changing feeders can then take care of starting to supply the new components into the machine.
Changing-over the screen printer is a more complicated procedure that typically involves removing paste from the stencil, cleaning it, removing and replacing the stencil, reconfiguring push-up pins, and resetting the squeegee.
Figure 1 describes the complete sequence of actions required.
To complete the changeover, assembly must be halted and cannot recommence until all actions are completed. The entire process can take 10 - 15 minutes, as indicated.
Among these tasks, procedures like removing and replacing the stencil typically require the operator to be trained to perform the tasks satisfactorily.
Generally, automating the labor-intensive tasks associated with a printer changeover has proved complex and challenging.
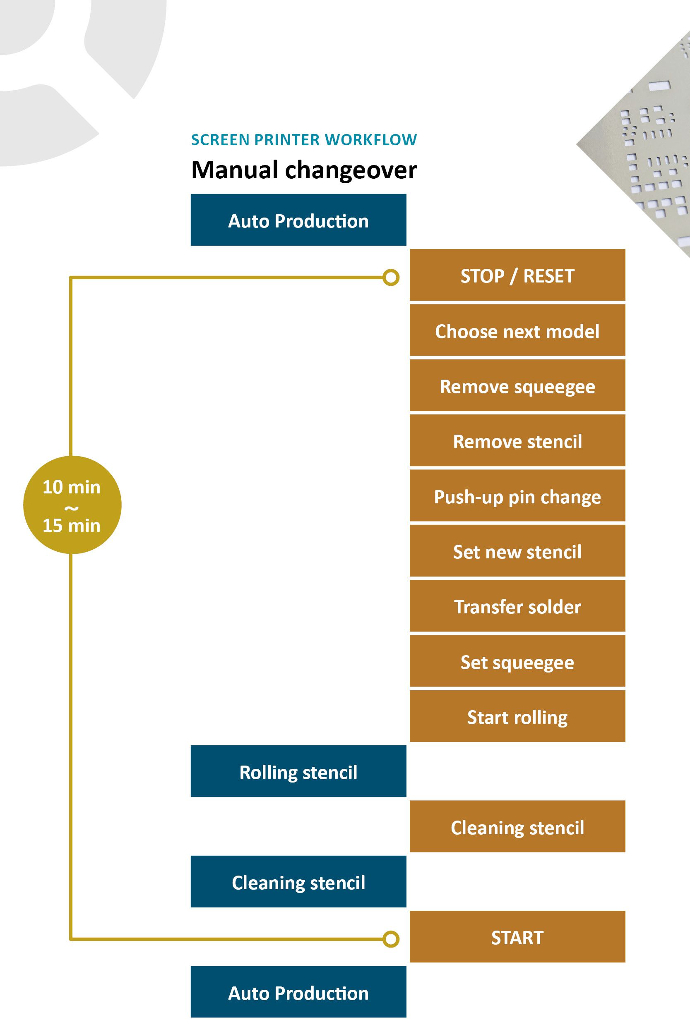
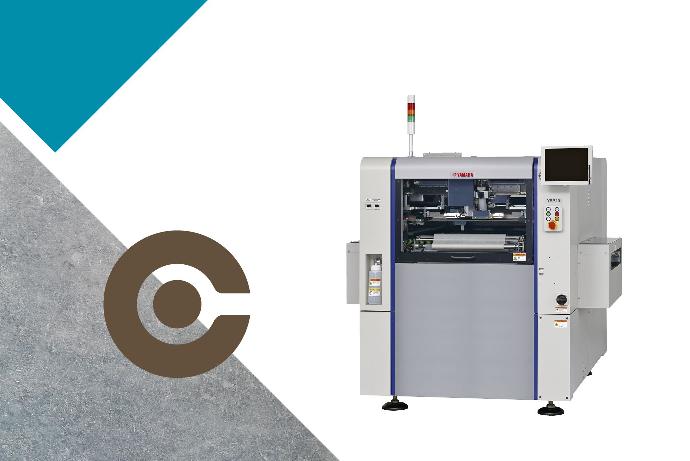
Now, by significantly re-engineering the internal structure of the standard screen printer, Yamaha has created the new Global SMT award winning YSP10 Screen Printer (figure 2) with automated changeover capabilities including:
stencil exchange
push-up pin exchange
and withdrawal & replacement of the solder paste roll onto the next stencil.
See Yamaha YSP10 specifications >
Figure 2. The Yamaha YSP10 printer, engineered for automated changeovers
Automated stencil and solder paste exchange
The entire changeover process can be completed in 3 - 5 minutes and production can resume immediately with no further checking, fine-tuning, or conditioning of solder paste required.
The sequence shown in figure 3 shows how the time to complete the changeover has been significantly reduced.
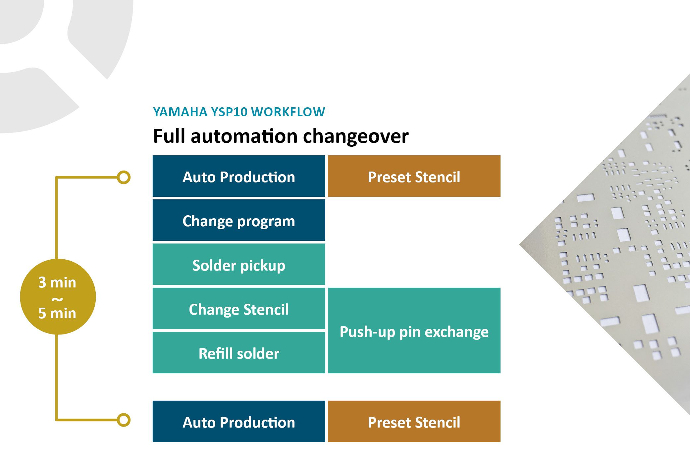
Yamaha YSP10 boost surface-mount productivity and accuracy with a combination of new and proved technology
Yamaha’s 3S (swing single squeegee) head (figure 4) allows optimization of the squeegee angle by servo adjustment to ensure optimum aperture filling. The squeegee angle is known to have a greater effect on aperture filling than other parameters such as speed and squeegee pressure. In particular, any solvent that may be present on the stencil surface immediately after a cleaning cycle has been completed can cause defective solder deposits on the first boards to be printed when operation resumes. The printer has a Filling Adjust System that automatically changes the squeegee angle to compensate for the differences in filling due to the solvent.
This helps to prevent printing defects without requiring extra action or delay for drying the stencil.
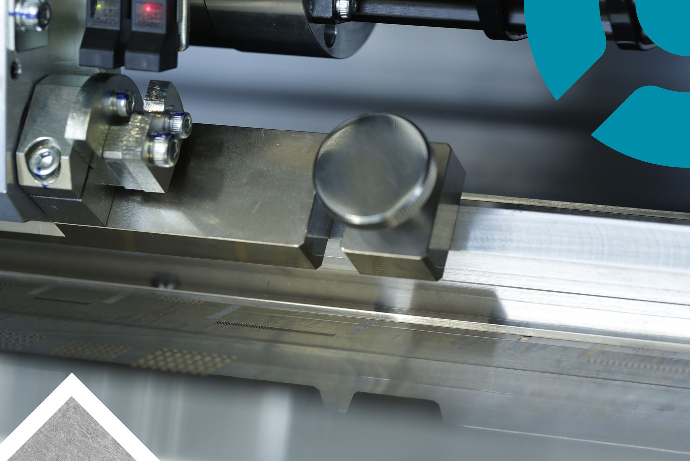
The head design works with unique squeegee technology that features a flexible blade of only 100 microns thickness treated with a 10-micron low-friction coating identical to that applied to the cylinder walls of Yamaha’s high-performance motorcycle engines to minimize wasted energy and extend durability. This coating effectively eliminates wear of the squeegee as well as the stencil, not only contributing to enhanced repeatability but also helping ensure improved results when printing with stepped stencils as well as lowering the overall cost of ownership of the printing process.
The combined effects of the squeegee and 3S head enable superior results when performing processes such as pin in paste. The printer can fill plated-through holes (PTH) with a single pass of the squeegee, whereas other systems that have a fixed angle and rigid blade may need to do several passes. Companies that need to ensure efficient pin-in-paste when building assemblies that contain, for example, large multi-pin through-hole automotive connectors appreciate the time savings and improved quality and repeatability that this system can deliver.
With the re-engineering of the printer’s internal layout to permit automatic stencil changeover, Yamaha’s vacuum-assisted stencil clamping mechanism helps ensure high positional accuracy and repeatability. The vacuum, applied to the stencil metal part, eliminates the effects of any distortion in the stencil frame and also minimizes any inaccuracies that can result from elongation of the mesh as the squeegee passes. Printing capabilities and the stability of solder-deposit shapes are both increased. In addition to the clamping mechanism, the printer’s graphical visual alignment system helps quickly and intuitively align the stencil and board, enabling perfect board-to-stencil alignment even when fiducials are poor or not present.
Features such as auto pin teach have become established over the past few generations of screen-printing machines. These simplify program generation by automatically determining the optimal positions for push-up pins to provide support during printing, using CAD information such as Gerber data or by using a high-resolution digital image of the board. The suite of tools that enable automated changeovers now adds automatic pin exchange to the printer’s capabilities, which further simplifies setting up tooling pins to support the new board.
Solder-paste roll handling is also automated to eliminate the inefficiencies when dealing with the remaining solder paste on stencil at the time of changeover. The paste is automatically removed from the stencil and retained, keeping the paste in its form as a roll. The paste can then be re-deposited on the new stencil surface after the changeover. Before re-commencing printing, the paste-roll diameter is measured and extra solder paste is added if needed, according to the print stability control (PSC) system. This sequence delivers two main advantages: operator contact with the paste is eliminated, and there is no time spent conditioning the freshly deposited paste roll. Printing can continue immediately, using the new program, as soon as the first board in the new batch enters the machine. The PSC system measures the paste roll diameter frequently during normal operation of the printer, which contributes to process repeatability by helping ensure consistent aperture filling.
User feedback; Accurate built-in inspection
A YSP10 printer user based in Belgium, operating a production line dedicated to automotive assemblies, found that the printer’s built-in (2D) two-dimensional inspection system showed comparable accuracy to that of a dedicated 3D solder-paste inspection (SPI) system.
Hence this built-in 2D system (figure 5) can ensure dependable solder-paste inspection results within the printer’s standard cycle time. With its 30 mm x 22.5 mm field of view (FOV), and with 18.7 µm resolution, this system can identify printing defects in fine deposit patterns for components such as small SMD chips and 0.5 mm-pitch BGAs.
The system provides automatic feedback to invoke stencil cleaning if paste-related problems are detected.
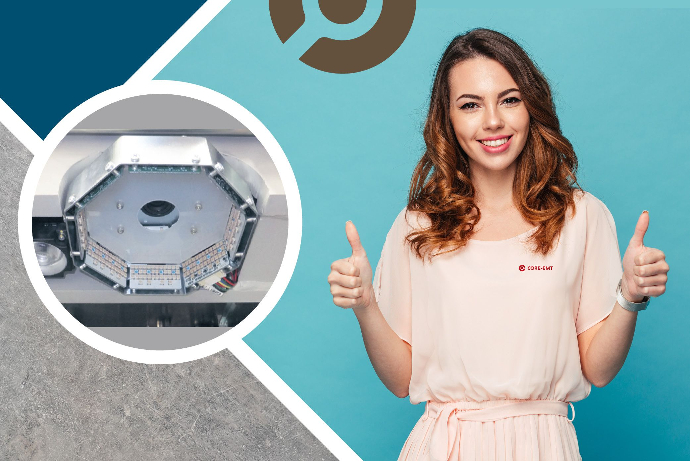
Conclusion
The tasks associated with screen-printer changeovers have historically been the most challenging to automate. While downstream aspects such as mounting and inspection have benefited from automation, changing over the screen printer has remained a labor-intensive task carried out by the operator.
This final frontier has now been conquered, enabling the automation of product-changeover tasks associated with all machines in the surface-mount line, resulting in greater productivity and quality.