From bulbs to boards: The shift to Surface Mount Technology in automotive lighting
Europe’s automotive lighting industry is undergoing a interesting transformation, moving away from traditional electrical production techniques and embracing high-speed precision electronics assemblies
In recent years, LED lighting has completely changed how vehicles look and how well they light up the road. You can see the difference in the bold new LED light designs, shapes, and branding on car lights, both front and back. Cars are now more brightly lit and visible, day and night, with sharper, whiter headlights that clearly illuminate the road ahead.
Inside, LED lighting also allows for customizable mood lighting, giving passengers control over the car’s interior ambience.
This shift to LED lighting has also transformed how these lights are made. Instead of traditional methods, modern LED light engines now involve complex arrays of LED emitters, along with the necessary power supplies and control electronics. These components are assembled using advanced surface-mount technology, either on PCBs or flexible circuits. This is a big step forward from older production methods, requiring precise automation to ensure everything is assembled perfectly.
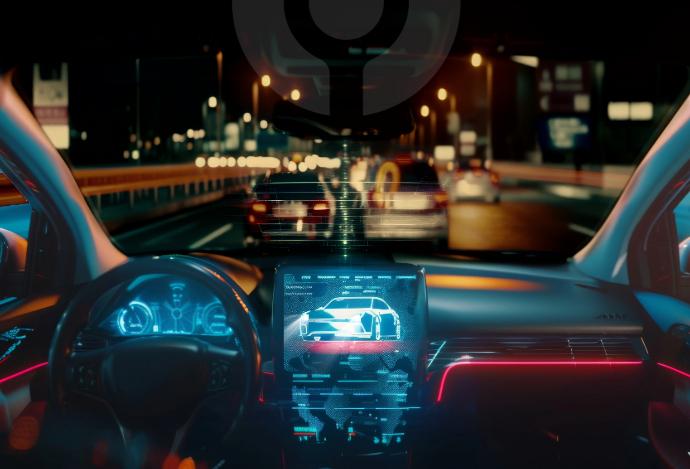
Europe’s automotive lighting industry is now embracing this change, moving away from traditional electrical techniques and adopting LED lighting created with precision electronics production. The LED lighting revolution isn’t just changing the look of cars; it’s also reshaping how automotive lighting is produced.
From bulbs to boards
High standards for automotive assemblies lighting
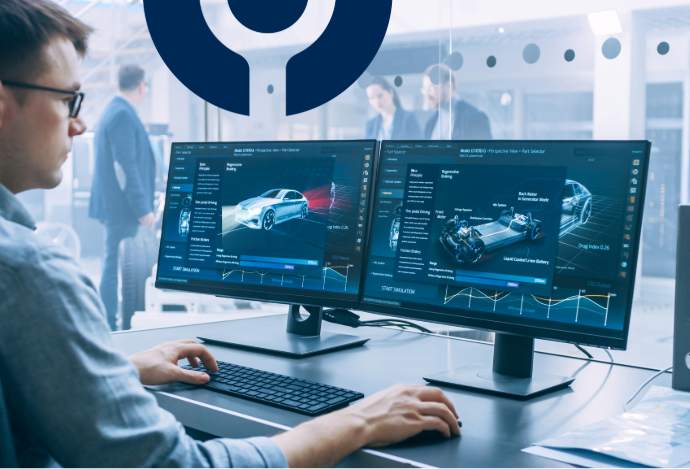
Automotive lighting assemblies demand an uncompromising level of precision and quality. Carmakers apply strict specifications for all components, and delivering high-volume production at the required standards is critical to keeping vehicle assembly lines running smoothly.
Many companies that now adopts new SMT techniques, have long histories in the automotive sector, producing conventional lighting products for decades. These companies are upgrading their design and production capabilities with new tools like computer-aided lighting software and simulation techniques to meet the challenges posed by LED assembly. While others are taking their very first steps into surface-mount electronic manufacturing.
According to Shuichi Imai, SMT Sales General Manager at Yamaha Robotics, customers are seeking automated, high-speed equipment that can handle fast component placement with minimal downtime due to fast product changeovers and robust traceability systems - essential in the automotive industry.
The shift to Surface Mount Technology in automotive lighting
How Yamaha's SMT solutions are powering the shift to LED automotive lighting
To meet these demands, Yamaha SMT utilize their full SMT line solution concept with a seamless workflow of screen printing, solder print inspection, component mounting and AOI inspection units. This integrated solution ensures seamless production, providing real-time diagnostics & reporting that keep operators informed.
Yamaha SMT machines are designed for ease of use and rapid changeovers, which is essential for manufacturers producing a variety of lighting products. The YRP10 screen printer features a cycle time of just five seconds and an intelligent squeegee system that optimizes itself. Meanwhile, the YRM20 mounter can handle a wide range of components with speeds up to 115.000 components per hour.
For those working with LED arrays, the Yamaha’s YRi-V AOI system offers advanced capabilities such as multi-component alignment checking, ensuring that all LEDs are correctly positioned, significantly improving quality control.
Setup your production for the future
Fast, flexible & scalable LED production
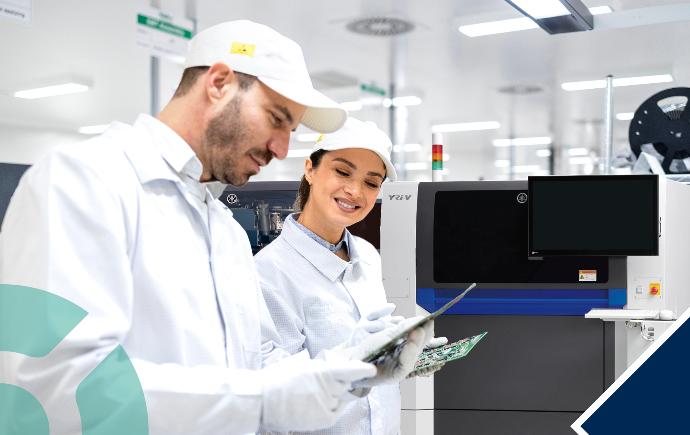
The YRi-V 3D AOI system, for example, delivers high-speed, accurate inspections and can even be used as a standalone system to accelerate product introductions.
Yamaha's equipment is engineered for fast product changeovers, allowing manufacturers to produce a high mix of products and cater to diverse customer needs. The company’s flexible approach enables lighting manufacturers to expand their capabilities while meeting the high standards demanded by today’s automotive market.
Shuichi Imai concludes, “Our full SMT line covers all aspects of surface-mount assembly and inspection, offering tailored configurations to meet the specific needs of our customers. With Yamaha’s expertise and advanced technology, automotive lighting makers can successfully transition to high-speed, high-yield SMT production.”
The shift from traditional techniques to SMT is a leap forward for the automotive lighting industry, enabling manufacturers to produce high quality, advanced lighting solutions at scale. As LED technology continues to evolve, SMT will remain a key component in bringing the latest innovations to light.
Shining a light on SMT
Unlock new opportunities: automotive LED lights the way
As SMT assembly lines continue to evolve, integrating automotive lighting assemblies in your production, can open new business opportunities.
With cutting-edge solutions like Yamaha’s automated equipment, SMT operators can easily adapt to meet the rising demand for precision LED manufacturing. Embrace these advancements to keep your production line at the forefront of technology and efficiency.
#Fun fact
Modern automotive LED lighting can shine for up to 20.000 hours and uses less energy than traditional bulbs - making them a win for both innovation and sustainability.
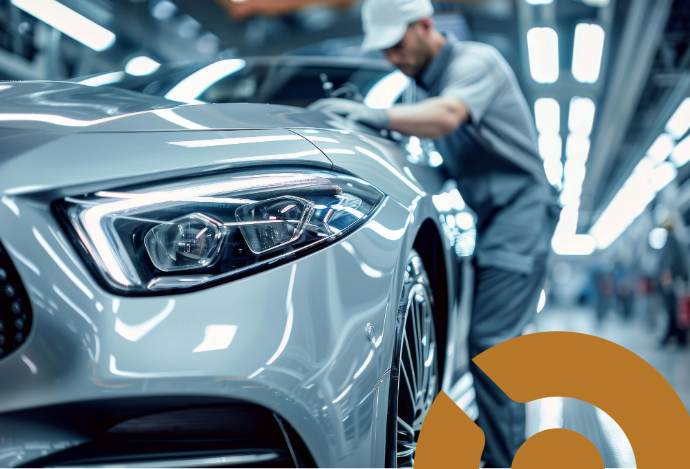