‘At our factory in Torsby we are, alongside – or maybe a little ahead – other serious EMS partners, in a constant process to improve and refine production stability, traceability, automated processes and handling to obtain high quality and fail-safe workflows.’
explain Marcus Eriksson, Production Manager at NOTE Torsby
The company, that is in rapid growth, found themselves increasingly challenged by their manual warehouse. Not only was material pick-up and return time-consuming, back and forward from their 3 assembly lines, there was also the risk of manually misplacing materials. Furthermore, the warehouse had large areas, that didn’t include humidity management for MSD components.
This led them to look closely into upgrading and how to optimize their manual warehouse.
’We knew that an advanced automated storage solution was needed. We were ambitious and the wish list was long.’ explain Marcus Eriksson, who continue ‘Naturally, storage of many reels – on a minimum of square meters – in a MSL controlled atmosphere was a must. The ability to connect to our factory software; SIMM and Material Manager was essential. And finally, we wanted to lift our storage workflow to achieve efficient quality-assured handling to bring our warehouse to the next level’.
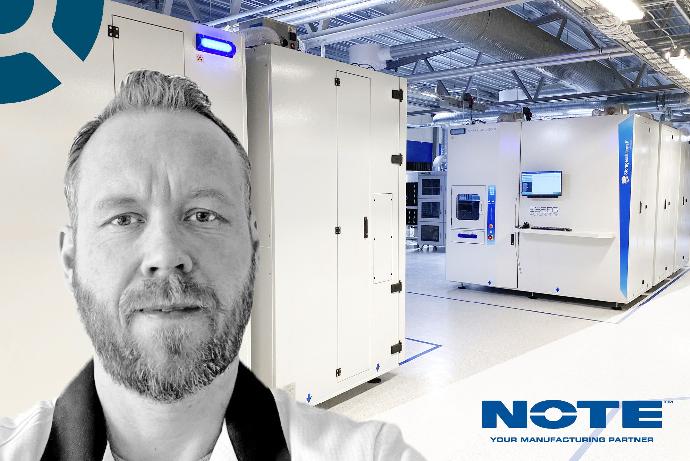
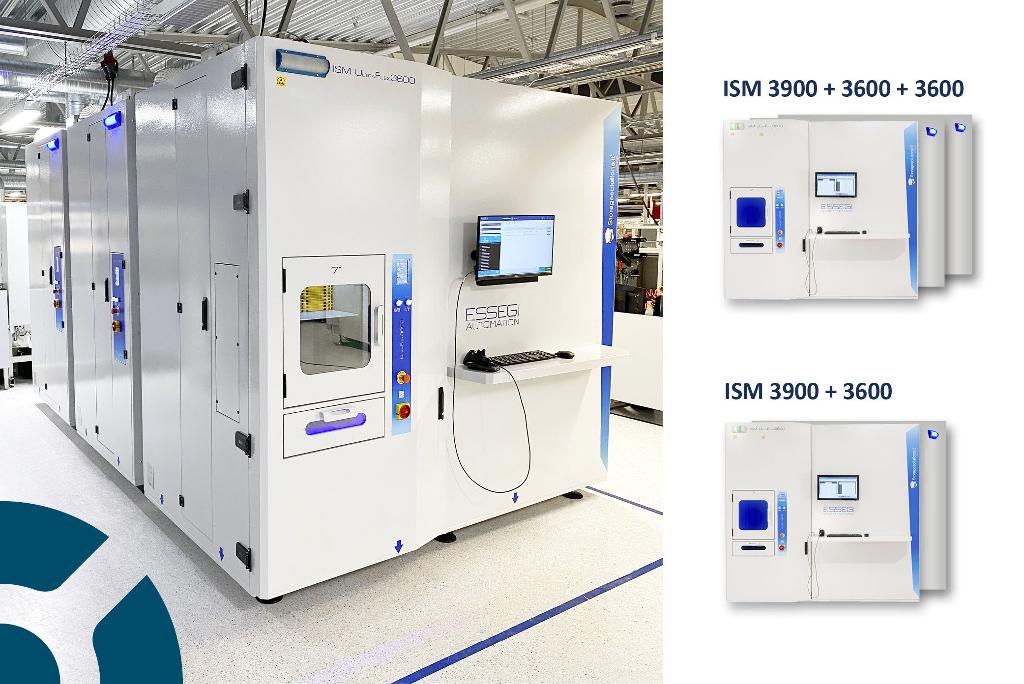
A new storage solution was installed at NOTE Torsby
Two Essegi Storage towers solutions that combine:
2 x front towers, ISM 3600 with
3 x tail towers, ISM 3900
Example: NOTES’ two new storage solutions, can store 18.900 pcs x 8 mm reels and takes up only 20 square meters in total.
Working with an
automated storage solution
Today the new storage workflow saves time, for the warehouse picking employees, and creates less material transport, as the towers automatically pick and return components. To verify the tower picked components, an employee scan a verification code on each picked material, before delivering them to feeder kit up.
When materials are returned to a storage tower, the warehouse employee can return up to 54 x 8 mm reels in one handling.
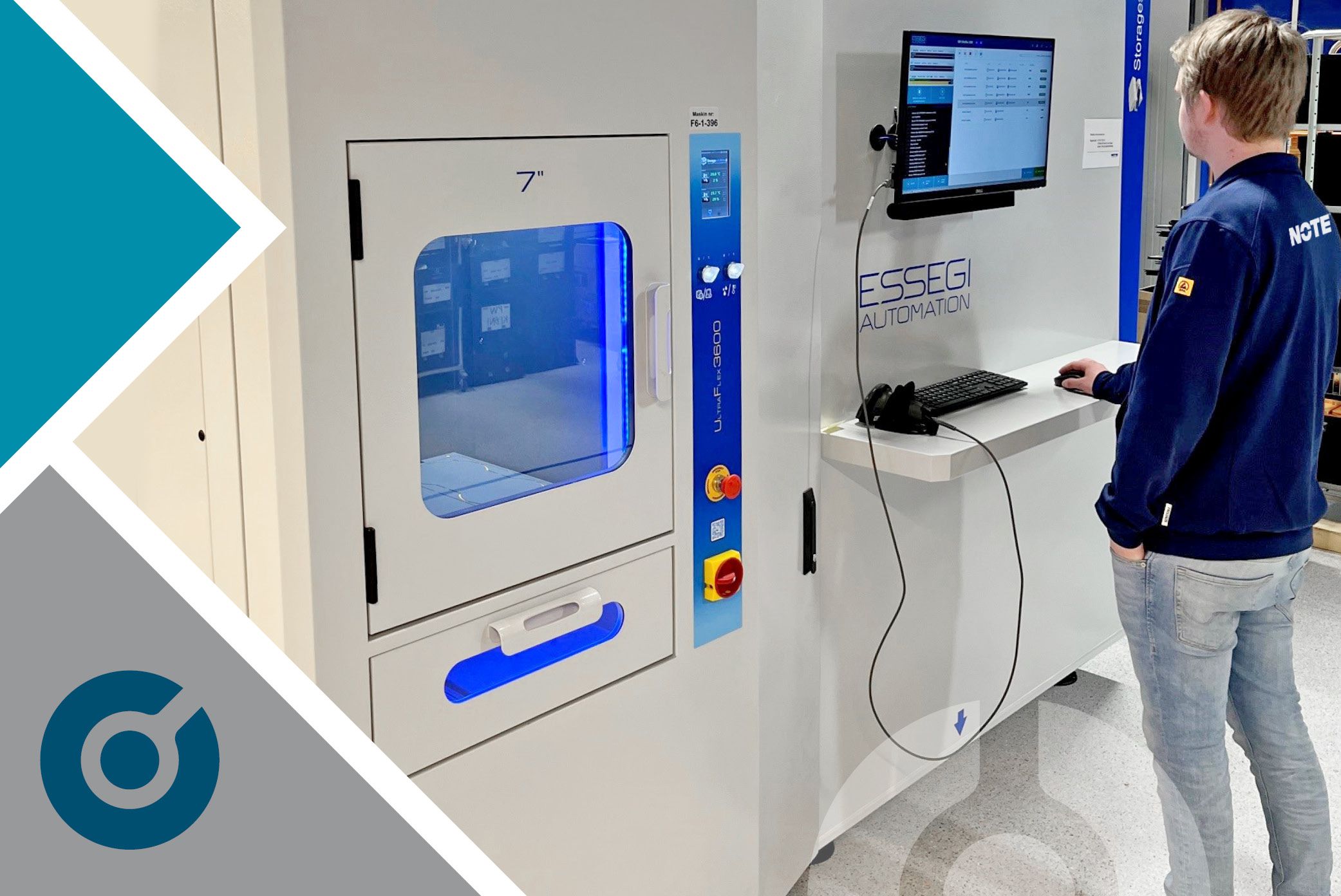
‘After only a few weeks, several of the warehouse issues we struggled with prior has been eliminated or greatly reduced. We also benefit from the more controlled material flow’ explain Marcus and continue
‘And as optimization is an ongoing process at NOTE Torsby, we are already investigating several features in the user-friendly Essegi Storage Solutions, which we eventually will implement to achieve greater automation and efficiency.’
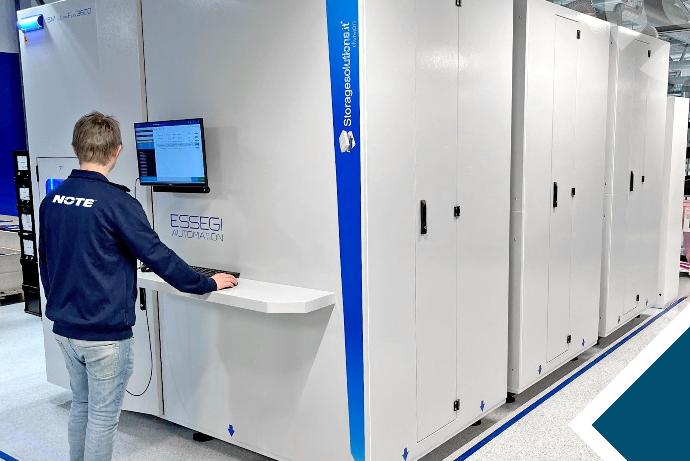
As stated on NOTE Torsby’s warehouse wish list, the new storage towers fulfill with e.g. MSD control, FIFO component handling, enables easy connection to the desired factory software, etc.
The new Essegi storage solutions to NOTE Torsby has been supplied and installed by CORE-emt.
‘CORE-Emt have been very helpful throughout the process. From the first meeting to complete installation. After this first collaboration between us we consider them to be a stable and serious supplier.’ ends Marcus Eriksson.
The NOTE EMS group
The NOTE Torsby factory is a part of the NOTE EMS group. One of northern Europe’s leading contract manufacturing partners for electronics and complete products. The NOTE EMS group covers everything from production technical services at an early stage to serial production and advanced after-sales services.