Configurate SMT mounters with mounting heads, feeders and nozzles
In SMT assembly, precision and efficiency depend on the key components of the pick and place process.
SMT mounters use
mounting heads, nozzles
and
feeders
to accurately pick, move and place components onto PCBs.
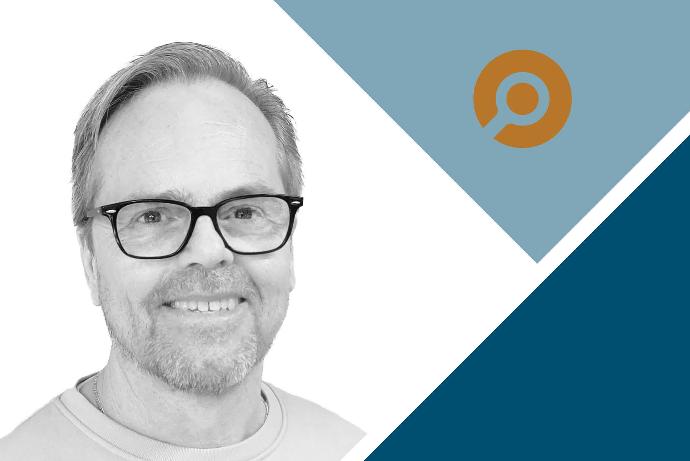
Need configuration guidance?
We offer expert guidance to setup and configurate your Yamaha SMT mounters with the best configuration for your production needs.
Understanding SMT mounters nozzles, mounting heads and feeders
SMT mounters play a key role in surface mount technology (SMT) assembly, ensuring precise and efficient component placement. To maintain high-quality production, it’s essential to understand the key components that drive performance: mounting heads, nozzles, and feeders.
How SMT mounters work
Pick and place machines, or SMT mounters, use a combination of mounting heads, nozzles and feeders to place surface mount components (SMDs) onto printed circuit boards (PCBs). The process involves:
- Component feeding
Components are supplied to the mounter via reel, tray, or stick feeders. - Component pick-up
Nozzles on the mounting head pick up components using vacuum technology. - Alignment & placement
Vision systems assist in positioning, and the mounting head precisely places the component on the PCB.
Types of SMT mounting heads
SMT mounters come with different mounting head configurations, each designed for specific production needs:
- High speed mounting heads
Optimized for placing small components at super high speed. - Flexible mounting heads
Designed for handling a wide range of component sizes, from microchips to large connectors. - Versatile mounting heads
Combines speed and flexibility for mixed-component assembly.
Understanding SMT nozzles
Nozzles are essential for accurate component handling and placement. The right nozzle choice ensures secure pick-up, proper alignment and defect-free placement.
- Standard nozzles
Used for common SMD components. - Custom nozzles
Designed for unique or delicate parts. - Nozzle maintenance & replacement
Regular cleaning and replacement prevent misplacements and production defects.
Choosing the right SMT feeder
Efficient feeder selection reduces downtime and improves line productivity. SMT feeders come in various types:
- Reel feeders
The most common, used for resistors, capacitors, and ICs. - Tray feeders
Ideal for handling large or sensitive components. - Stick feeders
Used for axial and radial components. - Smart feeders like the Yamaha ALF auto load feeder
Improve automation and reduce setup time.
Maintenance tips for SMT mounter components
To ensure smooth production, regular maintenance of mounting heads, nozzles, and feeders is essential:
- Clean nozzles regularly to prevent clogging.
- Inspect mounting heads for wear and misalignment.
- Calibrate feeders to prevent misfeeds and placement errors.
Optimizing your SMT pick and place process
To improve SMT line efficiency and accuracy, consider these optimization strategies:
- Use vision-assisted placement for better alignment and quality control.
- Upgrade to smart feeders for automated component tracking.
- Monitor placement data to detect trends in misalignment or defects early.
By optimizing these key components in your assembly line mounters, SMT manufacturers can achieve higher yield rates, reduce rework and maintain consistent quality in PCB assembly.